To make a complex
part in metal, you can cast it, forge it, stamp it, or machine it — or injection
mold it. Injection mold it? Yes. Injection molding by mixing metal powder with
plastic, molding it and then removing the plastic and sintering the part.
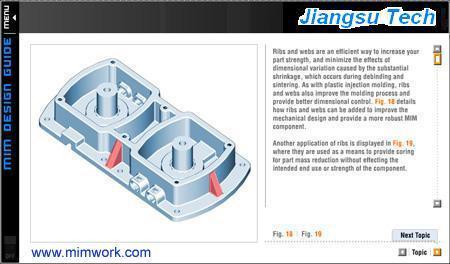
The process is
called metal injection molding (MIM), or sometimes powder injection molding
(PIM), and it can produce intricate parts in a wide range of metals, including
steel, stainless steel, and even high-temperature alloys. MIM has been around
for decades, but only in the last twenty years has found widespread commercial
application. Industries that now use MIM parts include aerospace, medical,
electronics, firearms and consumer products.
You may be
familiar with powdered metal, or PM parts, especially as bearings, bushings and
small gears. PM parts are formed of metal powder compressed in a die and then
sintered. There are several related processes that also use metal particles. MIM
uses much finer powder than PM, and a completely different manufacturing
process.
The worldwide
market for custom MIM parts is more than $500 million, according to James Dale,
vice president of member and industry relations, Metal Powder Industries
Federation (MPIF), Princeton, N.J. This does not include parts companies
manufacture for their own in-house use.
Since MIM can
be used to fabricate complex parts economically in structural metals, it can
provide significant cost savings to the savvy manufacturer. MIM can reduce part
cost in many cases. MIM can also make it possible to replace an assembly of two
or more parts with a single MIM part, eliminating the cost of assembling those
parts.
From powder to
part
MIM metal
powder is very fine, with particles 20 microns (about 0.0008″) in size or
smaller. “It feels like talcum powder,” said David Smith, senior sales manager
at PCC Advanced Forming Technology (AFT), Longmont, Colo. These very fine
powders are made by a number of processes, including atomizing molten metal with
a high-velocity stream of gas.
The MIM process
starts with mixing the feedstock, a combination of metal powder and binder. The
binder is a mixture of materials such as plastic and wax materials that melt and
hold the metal particles in suspension while the stock flows into the mold
cavities A typical feedstock might be 60 percent metal powder and 40 percent
binder by volume.
The feedstock
is heated and forced into the mold cavities. The parts are removed from the
mold. The newly molded parts are the shape of the final part, but larger. At
this stage they are called “green” parts.
The next step
is called first stage debinding. This removes most, but not all, of the binder
from the part. Debinding can be done with heat (thermally) or by a chemical
process, either with solvents or with chemicals that react with the binder.
After first
stage debinding, a small amount of binder remains to help the part hold its
shape. The part is now a “brown” part and is about 40 percent porous.
Finally, the
parts are set on ceramic trays, supported by fixtures if necessary, and placed
in a furnace to remove the last of the binder and sinter the parts. Sintering
may be done in a vacuum or in a hydrogen or other gaseous atmosphere, depending
on the requirements of the metals. For example, metals that form oxide on the
surface of the particles might be sintered in a hydrogen atmosphere to remove
the oxide layer.
In the
sintering furnace, the temperature rises until the remaining binder is gone and
the metal particles approach 90 percent of their melting temperature, at which
point they join together. After sintering, most MIM parts end up at 95 to 98
percent of full density; they contain 2 to 5 percent of equally dispersed voids
(pores). They have a smooth surface finish, typically around 32 RMS (root mean
square roughness).
MIM parts are
often used as-sintered, but machining, heat treating, plating and other
processes can be applied to the sintered part. Parts that distort during
sintering can be coined or otherwise straightened afterward. In special
applications where 100 percent density is required, a hot isostatic pressing
(HIP) process is used.
Economical for
small, complex parts in high volumes
Since MIM parts
are made in precision injection molds, similar to those used with plastic, the
tooling can be quite expensive. A MIM mold will cost about 20 percent more than
an equivalent plastic mold, according to Tim McCabe, technology development
manager, Kinetics Inc., Wilsonville, Ore. The MIM molds need to fit together
more tightly because of the properties of the binder compounds. Also, said
McCabe, in general, part tolerances tend to be tighter for MIM parts. The cost
of making injection molds varies tremendously and depends on many factors, but
tens of thousands of dollars would not be unusual for a multiple-cavity mold for
small precision parts.
To make MIM
economical, a company would need to amortize the tooling cost over all the parts
made. So MIM is usually used only for higher-volume parts. At his company, “
‘low volume’ is less than 10,000,” said McCabe, and typical quantities can run
to the hundreds of thousands, or even millions.
The MIM process
works best with smaller parts. Some typical maximum sizes listed by different
MIM shops are 100 to 200 grams (3.5 to 7 ounces), with a recommended size of 50
grams or less. One MIM manufacturer mentions its “rule of thumb” on its web
site: you can make MIM parts about the size of your thumb.
The mold is
designed over-sized to allow for the expected shrinkage of the part. Tolerances
on completed parts normally run in the 0.003”/inch range, with closer tolerances
possible. On longer parts, feature-to-feature tolerances can be challenging. In
this case, “you could mold in one hole and drill the other one,” said McCabe.
MIM’s niche in
the manufacturing world is small, complicated, high volume parts. Some parts may
not be economically viable without MIM. “MIM does not compete with pure
manufacturing,” said Smith. If a customer needs a part that could be a “straight
screw machine part, a stamping, or a powdered metal part, we’re not going to
compete.”
Material
mystery
The mechanical
properties of MIM materials can be close to those of wrought materials on
ultimate tensile strength. The small amount of porosity remaining in completed
MIM parts may impair dynamic properties such as impact and fatigue strength, as
compared with forged or wrought parts of the same alloy. However, the overall
uniformity and fine microstructure of the material can make for improved or more
consistent properties.
“One advantage
that MIM material has versus forged material is the lack of texture or
directionality of properties,” said Maryann Wright, engineering supervisor at
the Powder Metal Products Division of Remington Arms Company, Ilion, NY in an
e-mail interview. For wrought metals, the mechanical properties in the direction
of rolling can be different from the same properties in the transverse
direction. MIM parts are usually quite uniform in all directions.
MIM can also
have performance advantages over cast metals, which may have larger, irregular
pores and a non-uniform chemical composition due to the melting/ solidification
process.
Learning to MIM
Most of the
design guidelines for MIM parts are the same as for injection-molded plastic
parts. The same recommendations apply for uniform wall thicknesses and ribs for
strengthening. For MIM parts, you also need to think about how the part will
behave during sintering, and include design features to prevent sagging or other
deformation. Special fixturing can support the part during sintering, or the
part can be straightened afterward, but ideally it should support itself and not
deform in the sintering furnace.
Material
selection offers its own challenges. When working with a MIM house, you should
specify the mechanical properties the part needs to have, and let your MIM
supplier help you select the material on that basis. The alloy you end up using
for a MIM part may not be the same one you might specify for a cast or machined
part.
Experienced MIM
engineers can help fine tune a new design and select the right material. Also,
if you’re changing from a cast or machined part to a MIM part, or if you’re
creating a single molded part to replace an assembly, seek out the engineering
expertise at the MIM house. “The sooner you get the MIM designers involved, [the
better]. They may come up with solutions you may not have considered,” said
Dale. “[. . .] A MIM engineer sees problems every day that the design engineer
has never had to consider.”
A lot of design
engineers aren’t very familiar with MIM, said Dale. They may have heard
something about it in school, but may not have gone into any depth on the
subject.
To help remedy
this lack of exposure, Advanced Forming Technology conducts a “hands-on MIM
school” four times a year. Interested engineers, and a few purchasing people,
come to the plant and spend two days learning about MIM. They experience
first-hand how to mold, debind and sinter parts, and come away with a deeper
understanding of what MIM can do.
Though metal
injection molding is a powerful parts-making technique, it is not the ideal
method for making every part in every application. For some high-volume
products, however, MIM can solve design problems or save assembly costs in ways
not possible with other manufacturing technologies.
|