|
Ceramic Injection Molding (CIM) |
Ceramic Injection Molding (CIM)
Ceramic Injection Molding (CIM) excels at various engineering applications and
meeting material properties requirement such as chemical inertness, high
temperature stability, wear resistance and electrical insulation.
Ceramic injection molding (CIM) has been practiced for more than 30 years, but
has been restricted to niche applications with simple geometries such as the
ceramic cores for investment casting. The manufacturing process of CIM is
fundamentally similar to that of Metal Injection Molding (MIM), but contains
subtle and important differences in its processing parameters.
Jiangsu Tech is well positioned to overcome traditional manufacturing problems
via the CIM process with developments in binder technology, feedstock
productions, automated molding equipment, tooling design, sintering, and quality
control systems. This process will enable the cost-effective production of parts
with a range of geometric complexities.
The Ceramic Injection Molding Process
The CIM process begins with very fine ceramic powders. The powders are
compounded with polymer binders to produce a pelletized feedstock. During
molding, binders melt to form a liquid medium that carries the ceramic powders
into the mold during the injection stage.
Using an injection molding machine similar to that used in conventional plastic
molding, the feedstock is forced into a mold cavity forming a net shape part.
Molds can be single-cavity or multi-cavity configurations.
After forming, the part goes through a two-stage process. First is pyrolysis or
“debinding” to remove the binder, followed by sintering in a high temperature
kiln to form a fully dense ceramic component. Sintering is the process of
heating the material to a temperature below the melting point but high enough to
allow fusion of individual particles and densification of the material.
During sintering, the component shrinks by as much as 20% while retaining the
original geometric shape. With good process control, it is possible to achieve a
uniform and repeatable shrinkage leading to tight tolerances, obviating any need
for machining of the part afterwards.
Benefits of Ceramic Injection Molding
The well-known benefits of ceramic material include: high hardness and
mechanical strength; wear and corrosion resistance; dimensional stability over a
wide range of temperatures; ability to withstand high working temperatures; good
electrical insulation and excellent dielectric properties. However, until recent
advances in CIM technology, production engineers and product designers did not
view ceramics as a viable option for complex parts requiring tight dimensional
tolerances.
Combine ceramic materials and injection molding, and you get these benefits:
• Small, highly complex geometries you can’t get with other forming processes,
such as pressed powder and machining
• High strength
• Superior corrosion resistance
• Complex geometries without machining
• Excellent surface finish
• Overall part size and weight reduction
• Consolidation of multiple components into a single design
• Reduction of part count and assembly time
Ceramic has been a material of choice for demanding parts that require high
resistance to heat, corrosion, and wear. Today, Jiangsu Tech ceramic injection
molding (CIM) services make it possible to manufacture this durable material
into small and micro-sized parts with complex geometries.
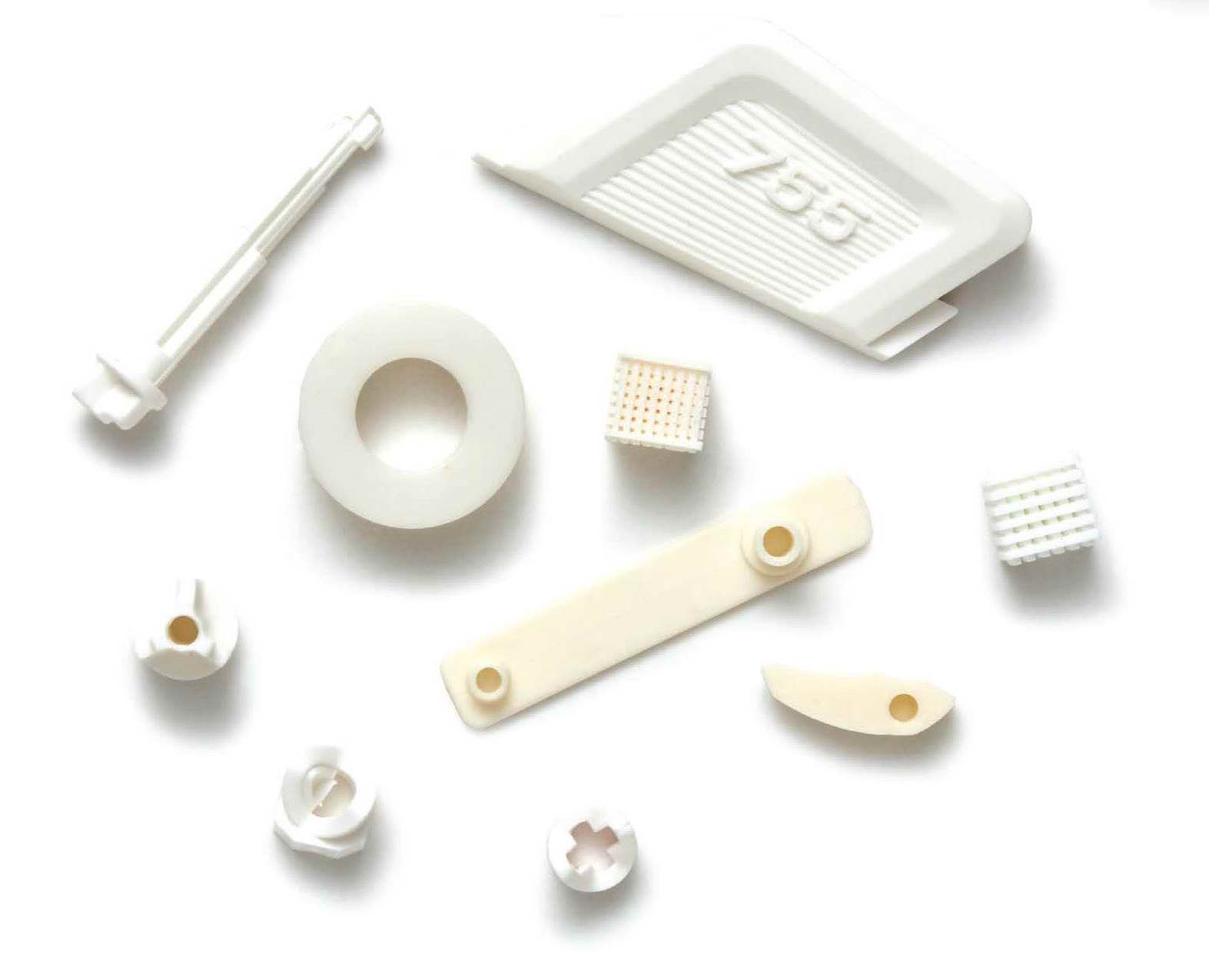 |
|
|
|
|
|
|
|
|
| |