The PM industry continued its growth track last year, and most indicators
signal a repeat performance in 2015. Metal powder producers, equipment
suppliers, and PM parts makers look ahead to favorable business conditions.
The
metal injection molding (MIM) industry, hot isostatic press (HIP)
business, and specialty PM products markets are gaining as well.
Metal powder shipments modestly increase
2014 North American iron powder shipments rose a modest 3.6% to 416,373
short tons. The PM sector of this total shipments figure increased by almost
4.4% to 376,944 short tons.
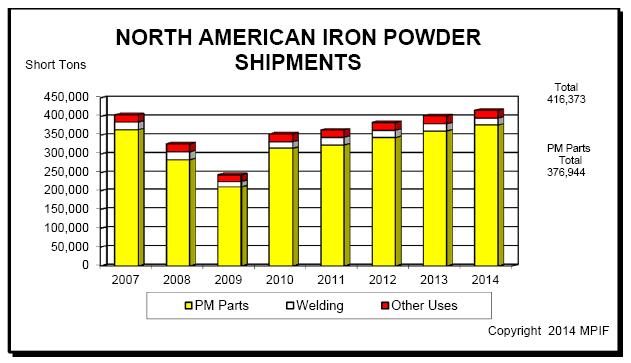
While iron powder shipments topped 400,000 short tons again, we must keep
in perspective the year 2004 when shipments hit a record 473,804 shorts
tons. Estimated stainless steel, copper, aluminum, nickel, molybdenum,
tungsten, and tungsten carbide powder shipments grew in 2014 as follows:
stainless steel 7,850 short tons; copper 17,500 short tons; aluminum 40,000
short tons; nickel 6,000 short tons; molybdenum 1,940 short tons; tungsten
3,600 short tons; tungsten carbide 5,900 short tons. Total estimated metal
powder shipments in 2014 increased by 3.4% to 499,213 short tons - see
below.
North
American Metal Powder Shipments |
|
|
|
|
|
|
2013 |
|
2014 |
|
Iron & Steel |
401,738 |
|
416,373 |
|
Stainless Steel |
7,600 |
(E) |
7,900 |
(E) |
Copper & Copper Base/Tin* |
16,850 |
(E) |
17,500 |
(E) |
Aluminum |
37,000 |
(R) |
40,000 |
(E) |
Molybdenum |
2,050 |
(E) |
1,940 |
(E) |
Tungsten |
4,200 |
(E) |
3,600 |
(E) |
Tungsten Carbide |
7,700 |
(E) |
5,900 |
(E) |
Nickel |
5,775 |
(E) |
6,000 |
(E) |
Short tons |
482,913 |
|
499,213 |
|
(E) Estimate
(R) Revised estimate
*PM parts only
PM equipment market overall
PM process equipment builders and tooling makers enjoyed a good year in
2014. PM parts fabricators are ordering new equipment for both capacity
increases and added capability, including more robotics and automation for
both compacting presses and sintering furnaces. There continues to be a
strong trend for larger compacting presses, over 500 tons, and presses with
more motions. Press shipments seem to be stabilizing at about 20 units
annually. In 2013 press shipments rose to 26 presses, with a backlog of 9
presses. In 2014 shipments declined to 19 presses, with a backlog of 11
presses at the end of the year.
Tooling orders remain positive. One major tooling company sees a growing
market for helical gears and a demand for finer and tighter dimensions,
especially on punch faces at +/- 10 microns after milling and polishing.
PM parts makers large and small are upgrading equipment. For example, one
major firm is phasing out older equipment in favor of new CNC equipment and
is considering acoustic blending equipment to achieve more homogeneous
powder mixes. Another smaller, family owned business will spend $3.5 million
on new equipment. These are positive signs reflecting the industry’s health
and boding well for future growth.
Current conditions and business outlook
Emerging from another good year, PM parts companies entered 2015
confident about positive growth indicators on the horizon, even spilling
over into 2017. A recent survey by the Powder Metallurgy Parts Association
reports that two-thirds of the respondents expect business to increase this
year.
Most PM fabricators are doing well, but there are still difficulties
finding qualified employees, especially die setters. The industry must do
more to attract skilled labor and engineering graduates into manufacturing.
MPIF recently participated in career fairs at several universities to
increase engineering students’ awareness of PM. MPIF staff engaged nearly
100 students while providing opportunities for possible employment.
North American iron, copper, and stainless steel powder shipments should
be up again in the three-to-four-percent range. Metal powder companies are
actively pursuing developmental projects to meet market needs and improve
the performance of raw materials through a reduction of lubricants in
binder-treated premixes and the use of a new lubricant for stainless steel
PM materials. A new generation of high-performance PM aluminum materials is
in the wings as well.
A number of key PM parts makers forecast double-digit growth this year in
both automotive and industrial markets. For example, new PM clutch designs
are taking hold in snowmobiles, snow throwers, and all-terrain vehicles.
PM’s high reliability in high-performance clutches is unquestioned, a
welcome sign and an example of the acceptance for PM components that are
used under harsh operating conditions.
Automotive trends
While a positive growth outlook remains in 2015 for PM in a potential
17.3 million car-year market, certain headwinds might diminish the pace of
this growth.
As we reflect on 2004, when iron powder shipments hit a record 473,804
short tons, we note that North American light-vehicle production was 16.2
million units. In 2014, auto builds advanced to 16.8 million units but iron
powder shipments reached only 416,373 short tons. A disconnect appears.
Several explanations suggest themselves. There is a new paradigm for
light-weighting in the automotive industry. Consider the example of the new
2015 Ford F-150 truck, which comes in at a weight of some 700 pounds less
than the comparable 2014 model; light-weight components such as its aluminum
body panels and high-strength steel ladder-frames come straight from
technologies used in the aerospace industry. The trend spawned by
manufacturers’ quest for higher CAFE numbers is toward smaller powertrains,
from eight-, to six-, and to four-cylinder engines, and thus toward fewer
and lighter-weight parts, and away from heavy PM bearing caps and
powder-forged connecting rods. PM, however, is not alone in feeling this
impact: competitive technologies such as castings, wrought forgings, and
machined parts must also pony up to meet rising technological requirements.
MPIF recognizes this light-weighting trend as an opportunity. As such,
MPIF has joined the Lightweight Innovations for Tomorrow (LIFT), an
industry-led, government-funded consortium, to help facilitate technology
transfer into supply-chain companies. LIFT is one of the institutes launched
by the National Network for Manufacturing Innovation. MPIF's move to gain a
voice in this $140+ million dollar program is important for our industry.
Another possible explanation for the disconnect between the increased
auto builds and the failure of powder shipments to rise to previous levels
is that many new engines and transmissions are being designed in Europe and
Asia with less PM content. The number of possible PM applications has
decreased. It is said European auto engineers lean towards higher
performance over cost and toward closer tolerances. For example, in North
America a Class 8 gear is normally acceptable, while European engineers
require Class 9 and 10 gears. Meanwhile, a leading German automatic
transmission supplier has designed an eight-nine speed transmission for a
Detroit 3 auto maker that contains only two PM oil-pump parts.
This trend has had the effect of forcing U.S. parts makers to meet
tighter or “Europeanized” tolerance requirements of less than 10 microns
across the board. Go-to trends for meeting these demands include surface
finish grinding, localized hardening, grinding after heat treating, and
grinding or machining for flatness.
Focusing on distinct PM product sectors with more value-added operations
is another trend involving big-name PM auto parts makers. For one
specialized automotive parts supplier, adding value through extra machining
and other specialized post-processing is enabling the company to book
business into 2020; the company is already in discussions about designs for
the 2021 model year.
PM content in light trucks amounts to between 55 and 60 pounds, with the
average PM content in light vehicles estimated at 45 pounds. This is in
marked contrast with the average European vehicle, which in 2014 contained
an estimated 21 pounds of PM parts.
The metal injection molding (MIM) industry has begun selling into the
automotive market. Automotive engineers are designing more MIM parts, which
points to significant potential growth as MIM becomes more accepted. MIM
parts are being designed for engines, electrical systems, and chassis
hardware.
Trends in metal injection molding, hot isostatic pressing and
additive manufacturing
Despite some bumps in the MIM business road, namely, the saturated
firearms market, 2014 was good to the North American MIM industry. The next
three-to-five years look positive as well. According to a 2014 survey by the
Metal Injection Molding Association (MIMA), the MIM industry is still
ascending its growth-cycle curve at a growth rate well above that of the
GDP. Some have even posited that the industry is still in the steepest
segment of its growth curve. The MIMA survey reported the following primary
end-markets in North America by weight of parts shipped: firearms, 28%;
general industrial, 24%; medical/dental, 19%; automotive, 15%; electronics,
9%; and miscellaneous, 5%.
While the firearms market currently remains somewhat sluggish, it will
most likely stabilize into a more normal growth pattern. However, overall
the MIM industry is set to enjoy a 10% growth rate in 2015, certainly an
enviable position.
The HIP market registered gains last year that should continue into 2015.
The use of PM HIPed products for the oil-and-gas market will increase,
despite declines in oil drilling and fracking. This is mainly due to long
lead times for necessary replacement parts. HIPed PM aerospace parts are
another growing market.
HIP densification of
MIM parts remains a robust growth business, and
there is new interest in HIP from the additive manufacturing (AM) sector.
Additive manufacturing offers an exciting niche business for PM and metal
powder producers. Without a doubt AM presents some very interesting
opportunities as a new PM technology. There are currently three well-known
commercial PM applications: titanium medical implant parts, cobalt-chrome
dental copings, and cobalt-chrome aircraft-engine nozzles made by GE at the
rate of 40,000 annually. RollsRoyce is also testing a prototype front
bearing housing made from a titanium–aluminum alloy for its Trent XWB-97
engines.
A number of powder makers are working on qualifying gas- and
water-atomized powders for AM applications made by laser-based,
electron-beam, and ink-jet processes.
Tungsten and refractory metals
The overall tungsten business faced tough times in the second half of
2014 due to weakening oil prices and mining activity. For example, total
tungsten powder shipments declined by 14.2% in 2014 to an estimated 3,600
short tons. Tungsten carbide shipments dropped 23.3% to an estimated 5,999
short tons. This year will remain rough as well. Oil-and-gas drilling,
important markets for tungsten, could drop by as much as 40 to 60%. The
outlook for mining, another well-established market for tungsten products,
will remain soft. The only bright spots are automotive and aerospace
markets, which unfortunately are not large consumers of tungsten.
MPIF & industry technology support
The MPIF Technical Board is reviewing the importance of reducing
dimensional variability in PM parts and taking a look at steps to improve
dimensional tolerances out of the compacting press. Board members are
gathering information about how process factors such as raw materials,
compacting, sintering, and secondary operations influence dimensional
control. The ultimate goal is to improve the dimensional tolerances of PM
parts by 50%. The board is also studying the development of lean alloys.
The Center for Powder Metallurgy Technology (CPMT), with its 52 industry
members, leads the investigation of strain-controlled fatigue for numerous
PM materials: resonant acoustical processing to enhance powder mixing;
sinter-hardening process improvements for flatness and throughput; die-wall
lubrication for warm compaction tooling; shot peening of gears for improved
performance; and ways to improve tooling to withstand compacting pressures
>60 tsi. CPMT is also providing $32,000 in university scholarships through
various family and corporate grants and sponsored four students to attend
POWDERMET2015 through another family grant.
Individual PM companies continue funding developmental programs aimed at
improved materials and processes to support PM’s growth and future
viability. Equipment makers, for instance, are designing more robust
multi-platen systems in both servo-controlled hydraulic and electrical
compacting presses. Higher-strength PM aluminum alloys are being developed
that provide yield strengths of 45,500 psi, as are high-density stainless
steels >7.4 g/cm3 by single pressing.
Novel R&D programs are being aimed at multiple-scale particulate
composites and combining metallic and ceramic properties, for instance,
joining the abrasion resistance and rigidity of ceramics with the toughness
and electrical conductivity of metals.
In conclusion, resilience and creativity are the hallmarks of today’s PM
industry. Just as it has survived and thrived in the face of previous
economic trials, these qualities will help insure that the industry will
continue to grow in the face of challenges yet to come.
This story is reprinted from material from MPIF, with editorial
changes made by Materials Today. The views expressed in this article do not
necessarily represent those of Elsevier.