|
News |
Award winning parts
highlight Metal Injection Molding’s global growth
25th Jul, 2017
The international Metal Injection Molding (MIM) industry once again
accounted for a significant proportion of the winning parts in the Metal
Powder Industry Federation’s (MPIF) 2017 Powder Metallurgy Design
Excellence Awards competition.
The winners were announced during the POWDERMET2017 International
Conference on Powder Metallurgy and Particulate Materials, Las Vegas,
USA, June 13-16, 2017.
These parts demonstrate MIM’s ability to deliver complex,
high-performance and cost-saving solutions for end-users in a diverse
range of end-user sectors, from automotive and aerospace, to medical
devices and firearms.
Grand prizes
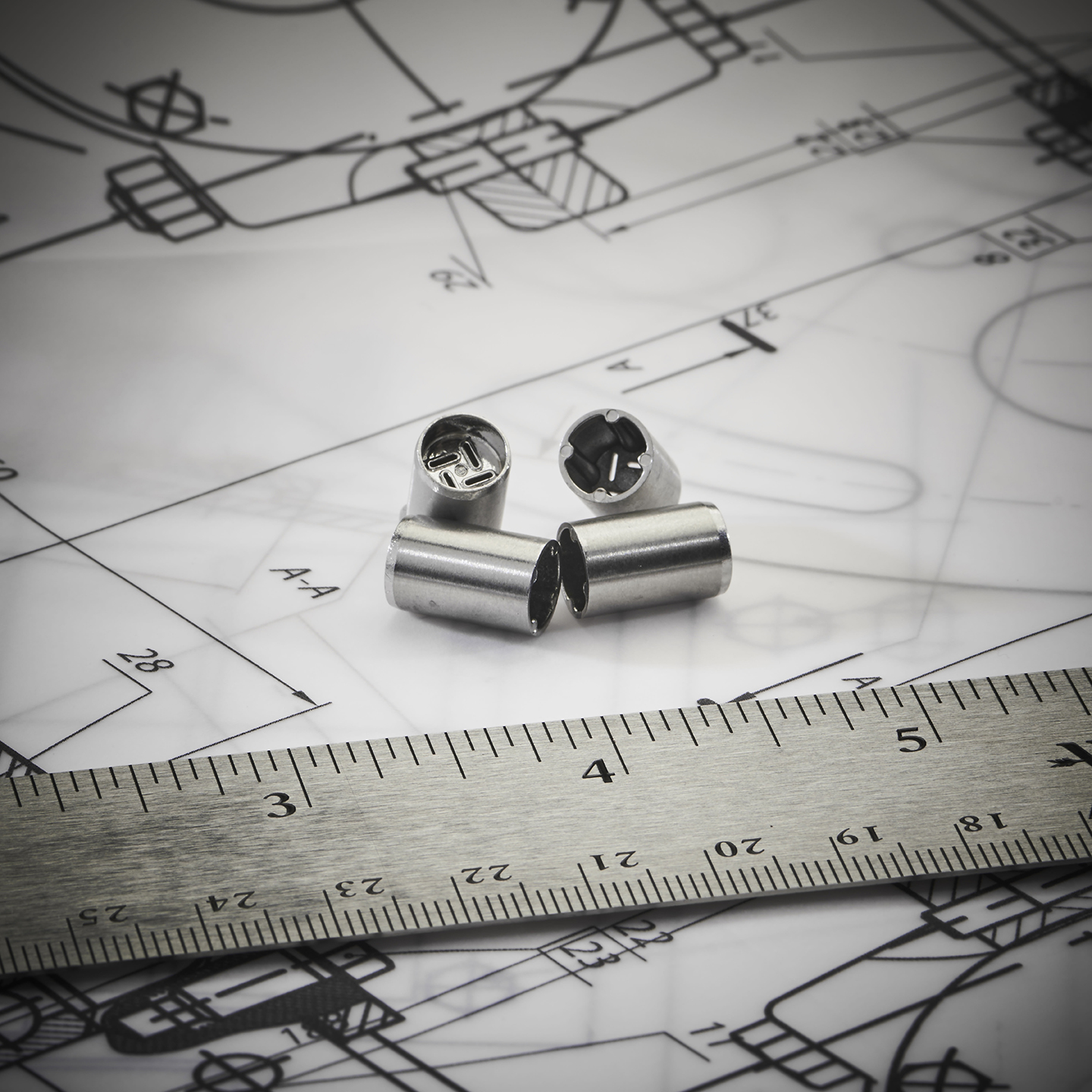 |
Grand Prize in the Automotive-Engine:
The
Grand Prize in the Automotive-Engine category is for a four-slot fuel
valve seat made for Delphi.
The Metal Injection Molded part goes into the Multec3.5 compressed
natural gas (CNG) fuel injector that satisfies the market’s need for a
low-cost, low-pressure port fuel injector.
It is currently used by several small-engine and automotive
applications, including aftermarket CNG conversions for trucks and cars,
helping contribute to a reduction in greenhouse-gas emissions.
|
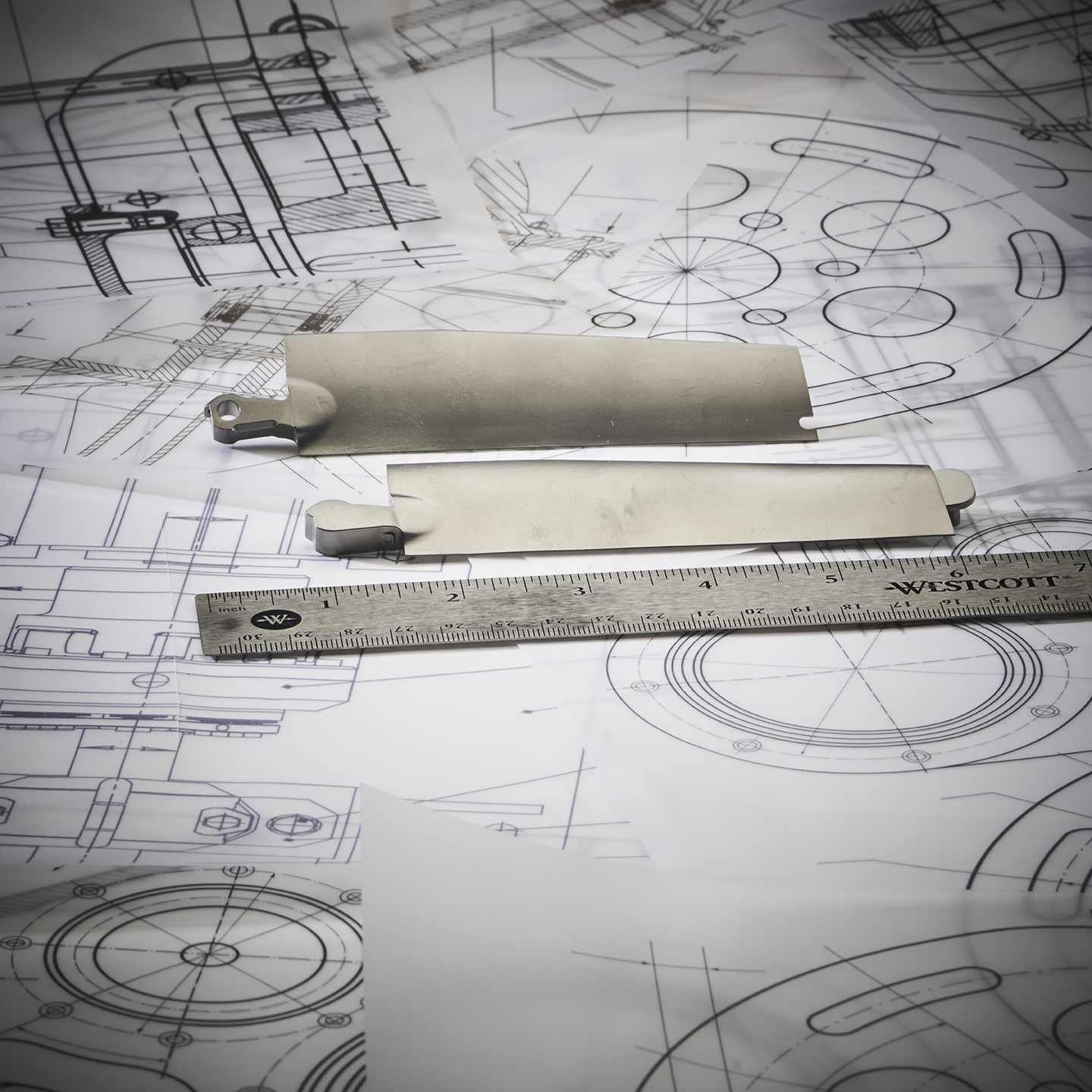 |
Aerospace/Military:
The Grand Prize in the Aerospace/Military category was made for UTC
Aerospace Systems and Raytheon Company.
The stainless steel part is used on the Talon, an add-on guidance and
control package that transforms a legacy 2.75-inch Hydra-70 unguided
rocket into a low-cost, precision-guided weapon.
Three canards on each Talon act as the primary flight control surfaces.
The Metal Injection Molded canard underwent a stringent qualification
process. |
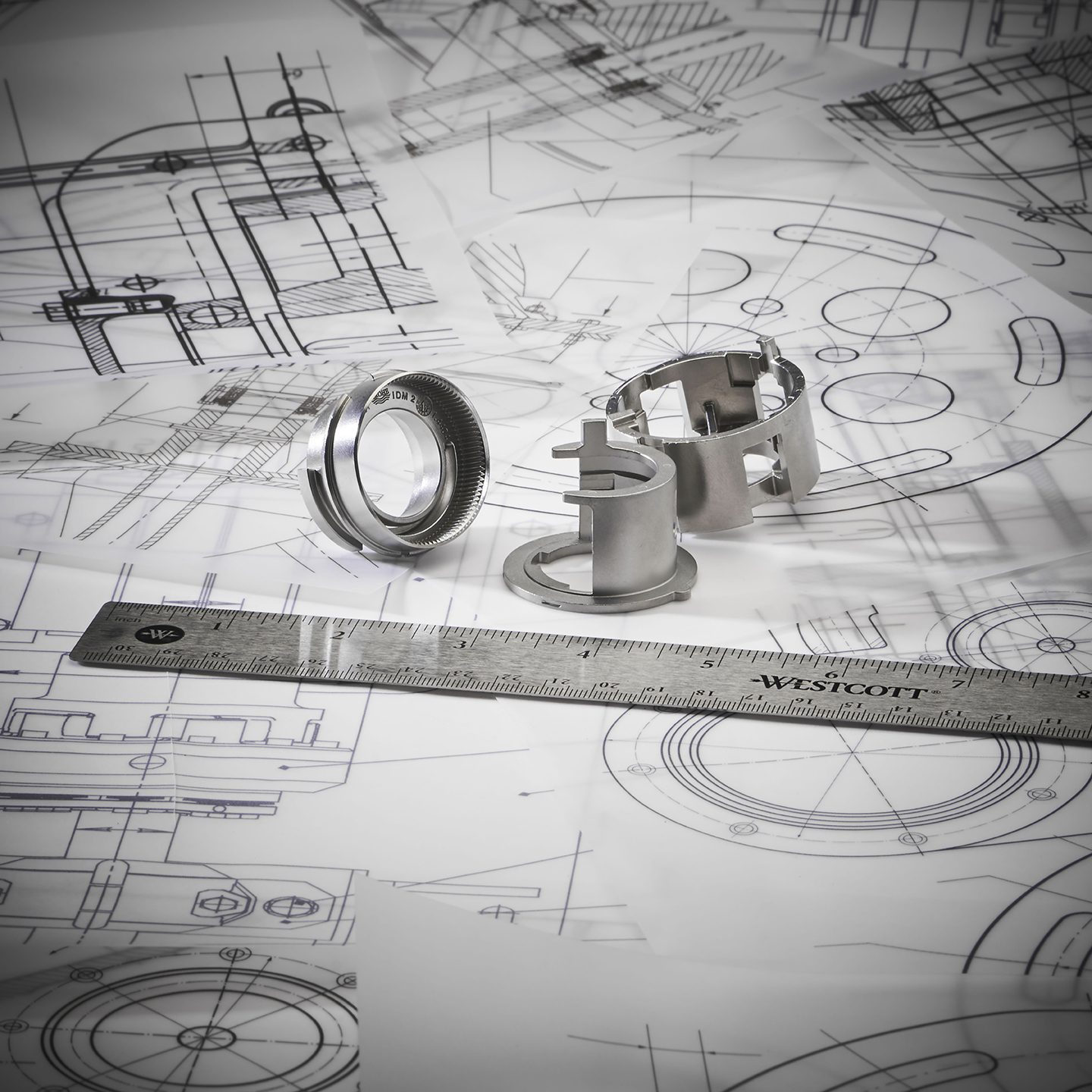 |
Hardware/Appliance:
The Grand Prize in the Hardware/Appliance category, for three Metal
Injection Molded parts—upper stop ring, stop ring and stop sleeve—made
for Grohe, Germany.
The parts go into the valve of a bath shower temperature controller
unit. Made of MIM-316L stainless steel, all three complex parts are
fabricated close to net shape and special ceramic setters are employed
for enhanced shape retention during sintering. |
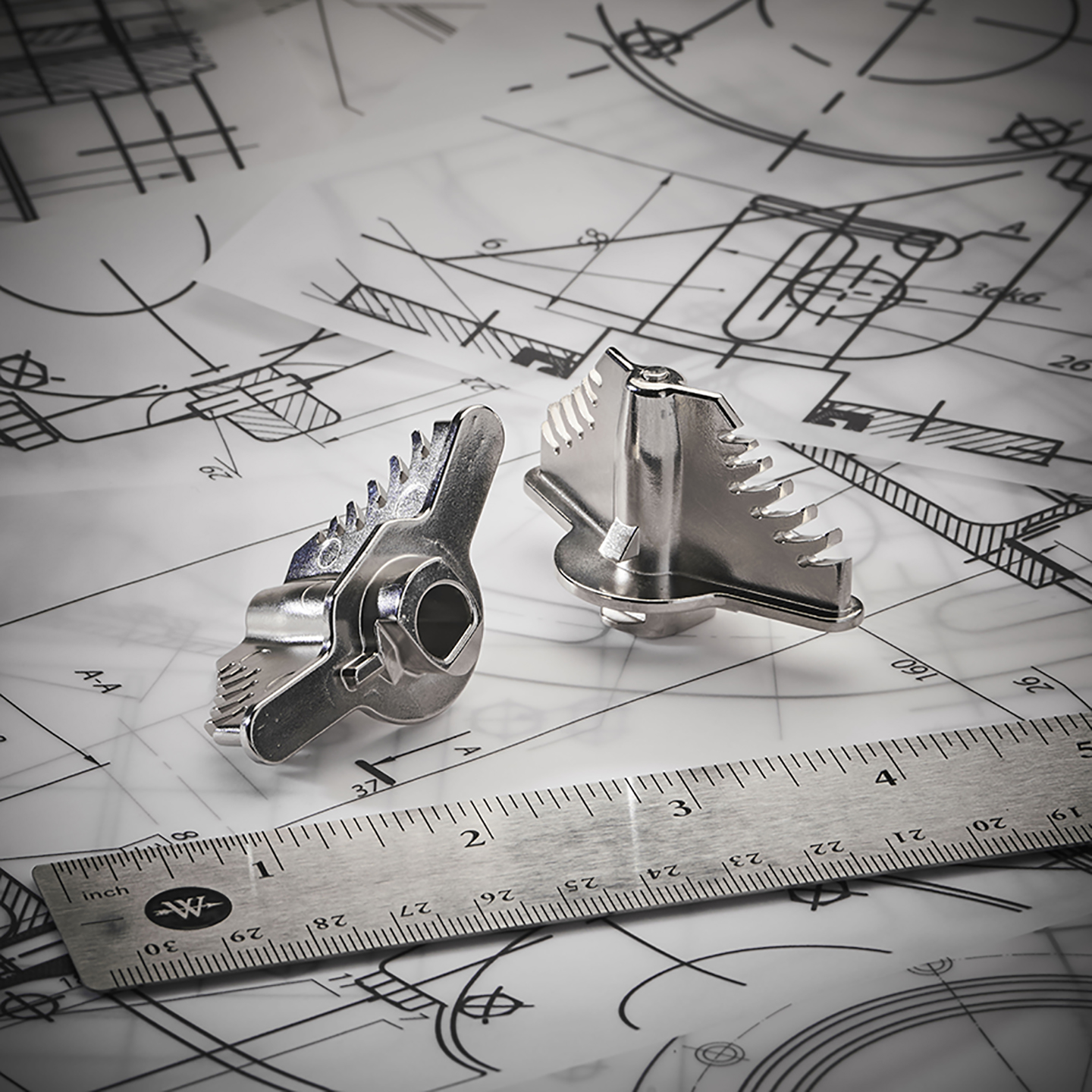 |
Medical/Dental:
The Grand Prize in the Medical/Dental category, for a Metal Injection
Molded surgical keel punch made for Paragon Medical.
The part functions as a broach to remove bone during knee surgery. Made
from MIM 17-4 PH stainless steel, the part is molded and sintered to
net shape with no additional coining, machining or other post-processing
to alter its shape. |
Awards of distinction
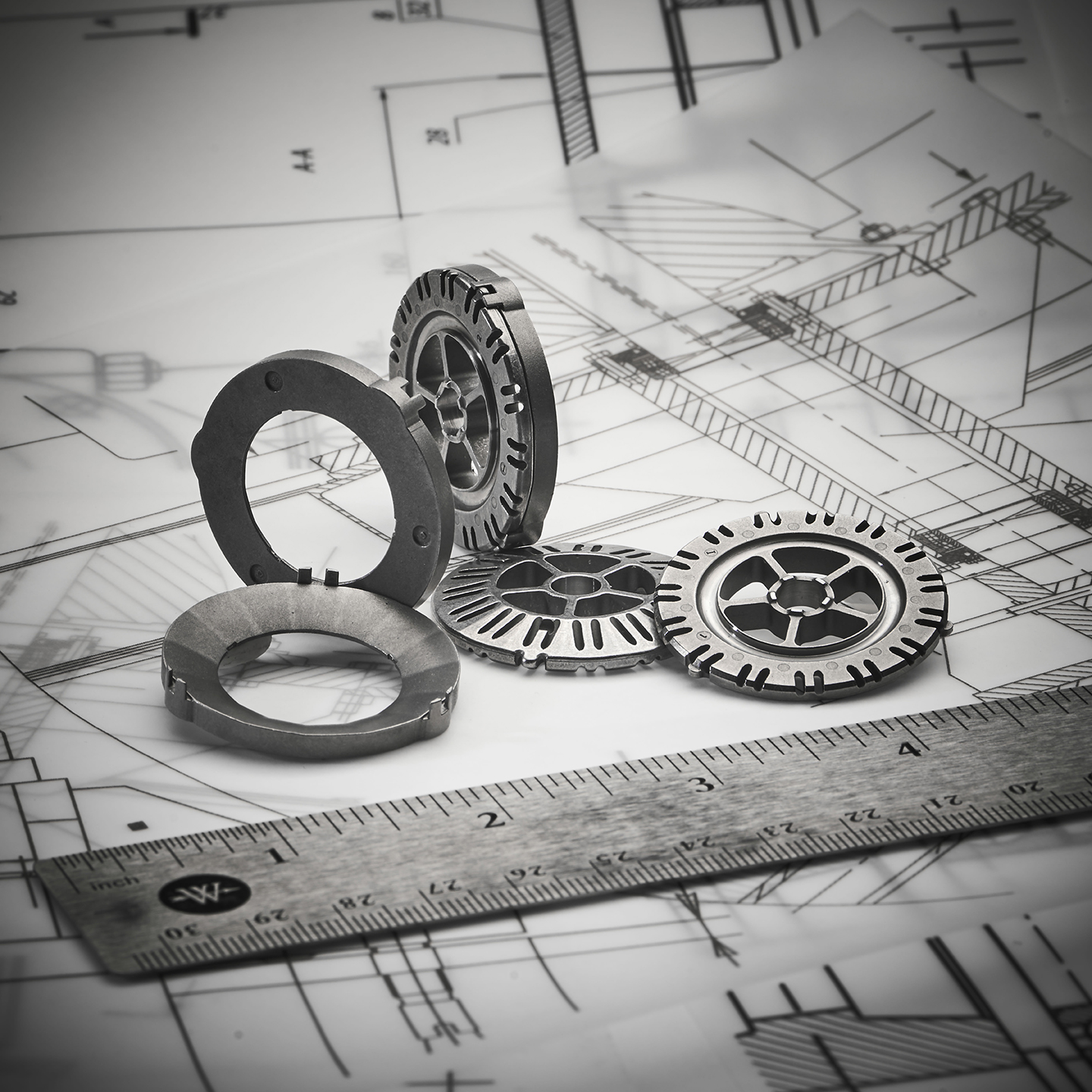 |
Automotive-Chassis:
Click for full size image
The Award of Distinction in the Automotive-Chassis category, for a
MIM-4605 low-alloy steel top plate and check shim stop made for its
customer Multimatic Dynamic Suspensions.
The mating parts go into shock absorbers on the Chevrolet Camaro sports
car. The Metal Injection Moulded design provided increased repeatability
and accuracy, providing an estimated 25% cost savings.
|
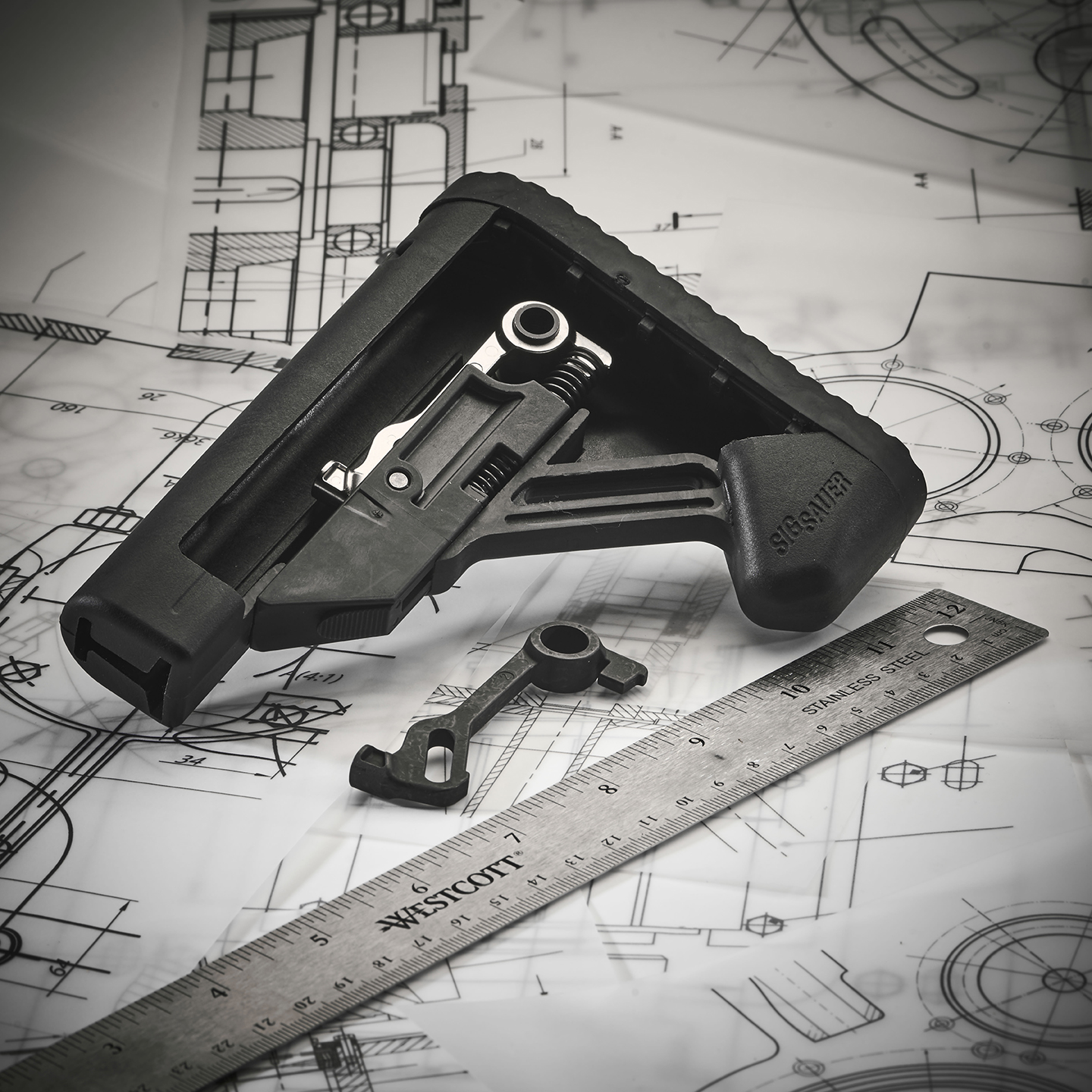 |
Aerospace/Military:
An Award of Distinction in the Aerospace/Military category, for a
MIM-4140 low-alloy steel latch made for Sig Sauer Inc.
The internal latch drives a subassembly for the telescoping feature of
the collapsible stock on MCX and MPX rifles. The part was designed for
Metal Injection Moulding as it could not be economically made using any
other fabrication method. |
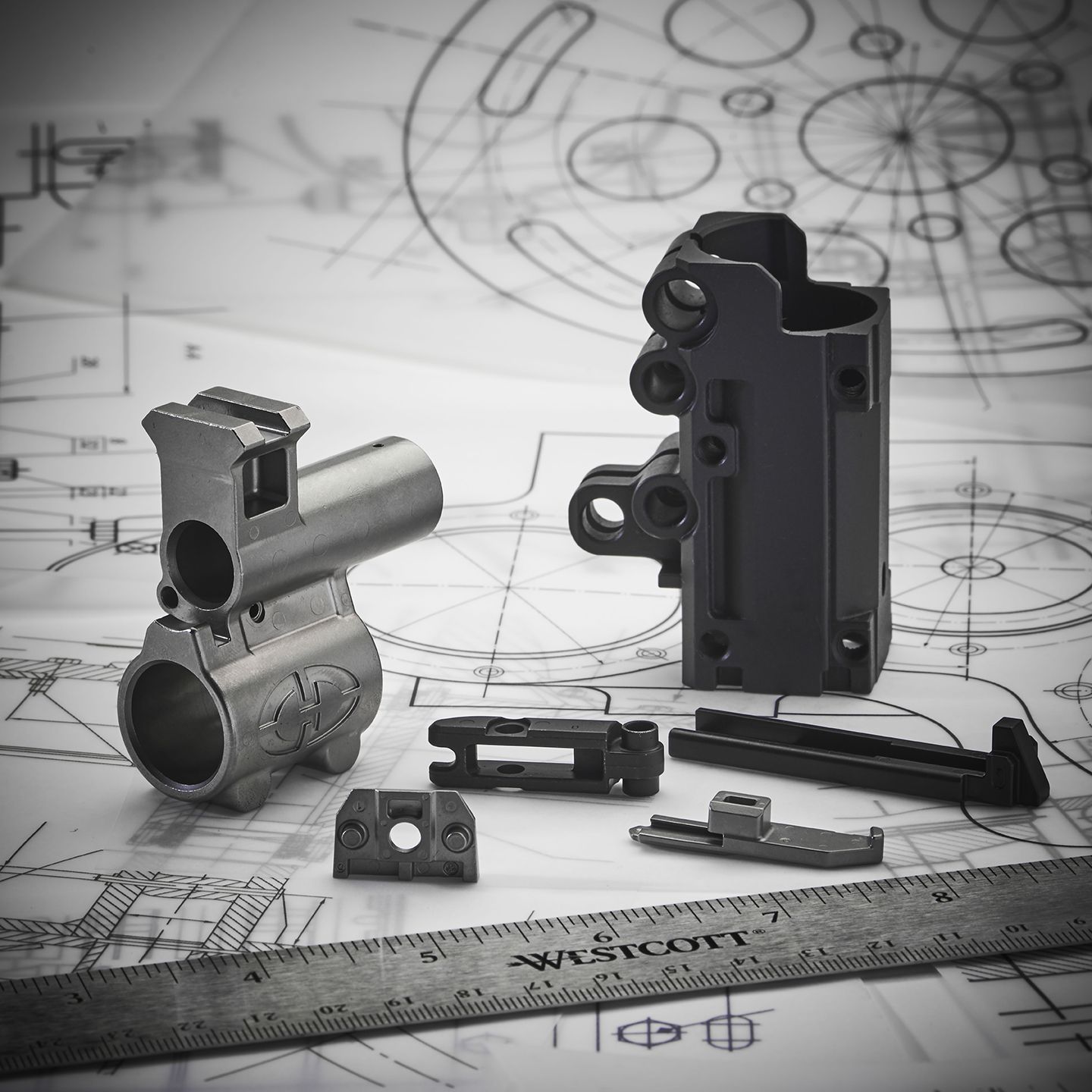 |
Hand Tools/Recreation:
An Award of Distinction in the Hand Tools/Recreation category, for a set
of Metal Injection Moulded parts, including a barrel block, gas block,
bolt catch, 7.62 NATO mag conversion bar, ejector retainer, and
extractor link, that go into an MDR rifle made by Deserttech.
The MIM-designed parts replaced ones that were machined, and reduced the
cost by 30% while manufacturing lead-time was cut in half. |
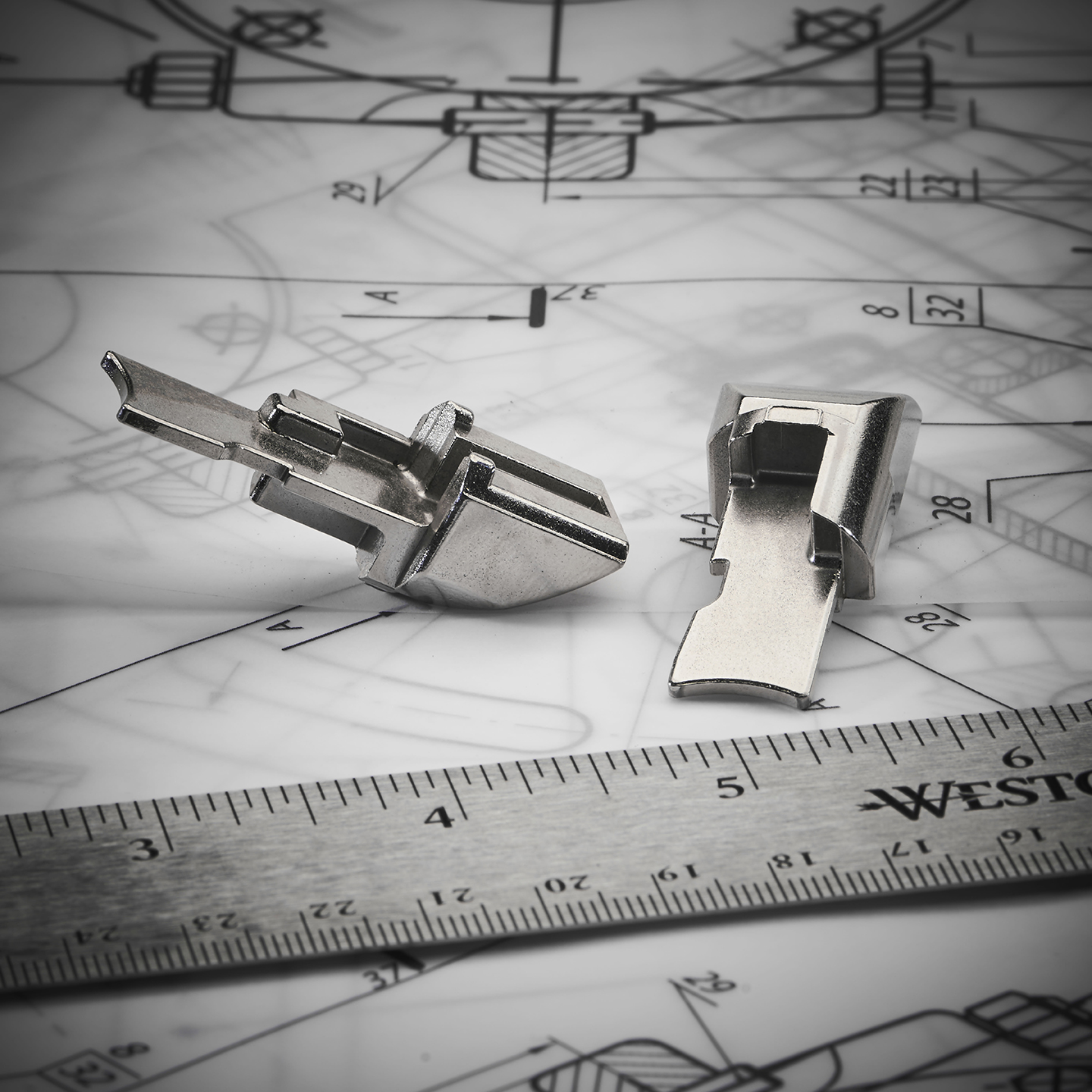 |
Hardware/Appliance:
An Award of Distinction in the Hardware/Appliance category, for a
copper-infiltrated steel bolt used in a commercial door lock system.
The part’s complexity, with its nine levels, rivals that which is more
typically seen in parts produced via MIM. The bolt is pressed and
sintered to its final shape without any secondary operations. It is
estimated to save 60% over the cost of other manufacturing methods. |
|
|
|
|
|
|
|
| |